En la industria electrónica en rápido desarrollo, el sustrato de alúmina se ha convertido en un sustrato indispensable para los componentes electrónicos con sus excelentes propiedades de aislamiento, estabilidad química, alta conductividad térmica y buenas características de alta frecuencia. No solo brinda soporte para componentes electrónicos, sino que también desempeña un papel clave en la disipación de calor y el aislamiento. Sin embargo, el proceso de preparación del sustrato cerámico de alúmina de alta calidad es complejo y delicado. Los factores clave, como la fórmula de la materia prima, el espesor de la película de fundición y los parámetros del proceso de sinterización, afectan directamente la uniformidad del espesor, la calidad de la apariencia y la rugosidad de la superficie del producto, y luego determinan el rendimiento general del producto. En este artículo, se analizaron los efectos de tres aditivos clave, aglutinante, plastificante y dispersante, y su control de proceso con el fin de proporcionar una referencia para optimizar el proceso de preparación del sustrato cerámico de alúmina.
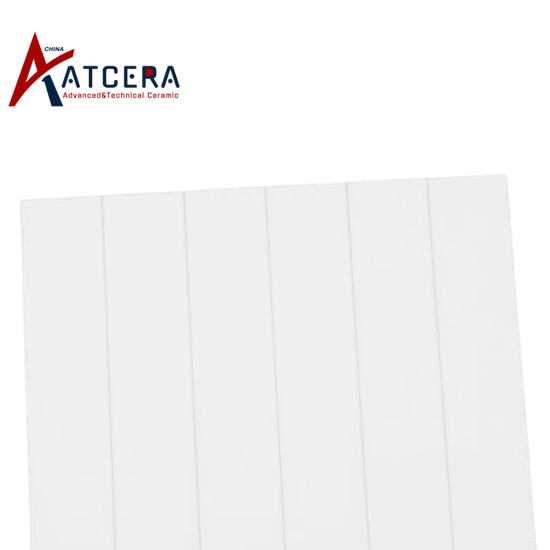
Selección de aglutinante y control de la cantidad de aditivo
Como aditivo orgánico clave para la construcción de redes tridimensionales de láminas cerámicas, los aglutinantes deben ser solubles en solventes seleccionados, y los tipos comunes incluyen polietileno, alcohol polivinílico, etc. El efecto de la apariencia, las características de procesamiento y la porosidad del verde de fundición La palanquilla sobre el rendimiento del producto debe considerarse de manera integral cuando se agrega la cantidad de aglutinante. La cantidad adecuada de aglutinante puede garantizar la resistencia y dureza del tocho verde, pero demasiado aglutinante provocará dificultades de desengrase y una disminución de la densidad del tocho verde, lo que afectará la tasa de contracción y las propiedades mecánicas del producto terminado. Muy poco no puede unir eficazmente el polvo.
Introducción y equilibrio de plastificantes
Al reducir la temperatura límite plástica del aglutinante, el plastificante mejora la flexibilidad y trabajabilidad de la película fundida, resuelve el problema de la dureza insuficiente después del secado y mejora la estabilidad de la suspensión. Sin embargo, la adición de plastificantes debe ser moderada para evitar una reducción excesiva de la resistencia de la película. El plastificante ideal debe tener propiedades fisicoquímicas estables que sean compatibles con otros ingredientes de la pasta, asegurando una adición mínima y manteniendo el rendimiento.
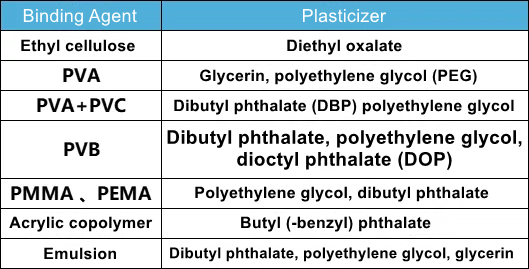
Los aglutinantes comunes corresponden a plastificantes
Selección y ajuste de dosis del dispersante
La buena dispersión del polvo en suspensión es la base para preparar un sustrato cerámico de alúmina de alta calidad. El agente dispersante promueve la suspensión de partículas a través de impedimentos electrostáticos y estéricos y se dispersa de manera estable. Dependiendo del sistema de lodo, es importante elegir el tipo correcto de dispersante (como dispersante inorgánico, orgánico, polimérico y compuesto). La cantidad de dispersante añadido se ajusta según el tamaño del polvo de alúmina y las partículas finas normalmente necesitan más dispersante debido a su alta energía superficial.
En resumen, la selección y control del proceso de aglutinante, plastificante y dispersante tienen una influencia decisiva en el rendimiento del producto final durante la preparación del sustrato cerámico de alúmina. La uniformidad del espesor, la calidad de la apariencia y la rugosidad de la superficie del sustrato cerámico de alúmina se pueden mejorar efectivamente regulando con precisión los tipos y cantidades de estos aditivos, combinados con el espesor optimizado de la película de fundición y los parámetros del proceso de sinterización de desviscosa, para garantizar su excelente rendimiento en electrónica. componentes. En el futuro, con el progreso continuo de la ciencia de los materiales y la tecnología de preparación, una mayor optimización de la formulación de aditivos y los parámetros del proceso abrirá nuevas posibilidades para la aplicación de sustratos cerámicos de alúmina en una gama más amplia de campos.