En el campo de la industria electrónica, el sustrato de alúmina se ha convertido en un material base indispensable para los componentes electrónicos debido a su excelente aislamiento, estabilidad química, alta conductividad térmica y buen rendimiento de alta frecuencia. No solo desempeña el papel de soporte y disipación de calor, sino que también garantiza el rendimiento de aislamiento de los componentes electrónicos. La lechada de fundición de alúmina es la materia prima clave para la preparación del sustrato cerámico de alúmina, y su composición y características determinan directamente la calidad y el rendimiento del producto final. El propósito de este artículo es investigar cómo las características del polvo de alúmina, incluida la pureza, el tamaño y la superficie específica, la morfología y la dispersión, afectan el proceso de fundición y el rendimiento del sustrato cerámico de alúmina.
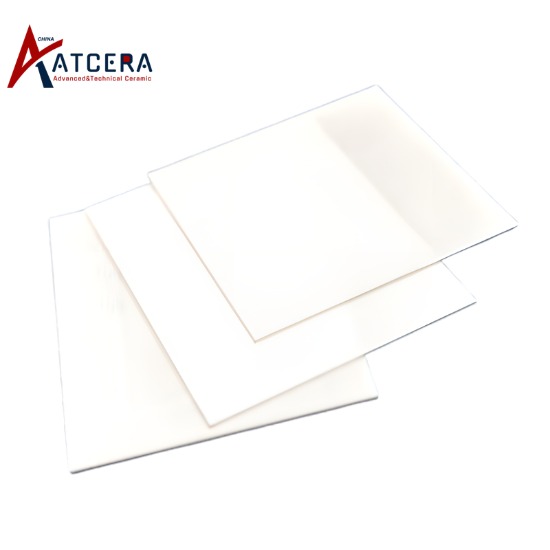
Efecto de pureza
La pureza del polvo de alúmina es la base de la calidad de la lechada de fundición. El contenido de alúmina requerido generalmente no es inferior al 95 % para evitar el impacto negativo de las impurezas en la apariencia, la contracción, la microestructura y el rendimiento del producto terminado. Por ejemplo, los polvos de óxido de aluminio que contienen partículas de Fe libres provocarán el desarrollo de color dentro o en la superficie de la cerámica durante el proceso de sinterización, formando manchas que no solo afectan la apariencia, sino que también reducen el rendimiento del aislamiento.
El efecto del tamaño del polvo y la superficie específica
El tamaño del polvo de alúmina se controla en el rango de 0,3-1,7 μm, y el área de superficie específica está entre 2-11 m²/g, lo que tiene un impacto importante en la densidad del producto terminado. El polvo de tamaño de partícula pequeño tiene mayor área superficial y energía superficial, lo que favorece la densificación de la película fundida. Sin embargo, un tamaño de partícula demasiado pequeño aumentará la necesidad de aditivos como dispersantes y aglutinantes, deteriorará la fluidez de la lechada, aumentará la contracción de sinterización y reducirá la densidad de sinterización.
Efecto de la morfología del polvo
La morfología del polvo de alúmina es variada, incluyendo esférica, en escamas, fibrosa e irregular. Debido a su superficie lisa y buena fluidez, las partículas esféricas favorecen la mejora de la densidad del producto terminado. Por el contrario, es fácil que las partículas no esféricas formen espacios después de la sinterización, lo que afecta el proceso de densificación.
Optimización de la descentralización
Mejorar la dispersión del polvo en la suspensión es la clave para garantizar la calidad del producto terminado. Además de la adición de dispersantes, el tratamiento de modificación de la superficie del polvo, como la modificación química o el tratamiento físico, puede mejorar significativamente la dispersión y las propiedades reológicas de la suspensión, para optimizar el proceso de fundición.
En resumen, las características del polvo de alúmina juegan un papel crucial en el proceso de fundición de la preparación del sustrato cerámico de alúmina. Controlando estrictamente la pureza, el tamaño, el área superficial y la morfología del polvo y optimizando la dispersión, se pueden mejorar significativamente los indicadores clave de rendimiento como la conductividad térmica, la resistividad, la constante dieléctrica, la estabilidad química y la resistencia mecánica del sustrato cerámico de alúmina. En el futuro, con el progreso continuo de la ciencia de los materiales y la tecnología de preparación, el estudio en profundidad y la regulación fina de las características del polvo de alúmina promoverán aún más la aplicación y el desarrollo de sustratos cerámicos de alúmina en el campo de los componentes electrónicos de alta gama. y proporcionar una base sólida para el desarrollo sostenible de la industria electrónica.