Con el progreso continuo de la tecnología de embalaje de microelectrónica, la potencia y la integración de los componentes electrónicos han aumentado significativamente, lo que ha llevado a un aumento significativo en la generación de calor por unidad de volumen, lo que ha planteado requisitos más estrictos para la eficiencia de disipación de calor (es decir, , su rendimiento de conducción de calor) de la nueva generación de placas de circuito. En la actualidad, los investigadores están trabajando para desarrollar una variedad de materiales de sustrato cerámico con alta conductividad térmica, incluido nitruro de aluminio (AlN), carburo de silicio (SiC) y óxido de berilio ( BeO). Sin embargo, el BeO tiene limitaciones medioambientales debido a su toxicidad; El SiC no es adecuado para su uso como material de sustrato debido a sus altas propiedades dieléctricas constantes. Por el contrario, el AlN es el material de sustrato preferido debido a su coeficiente de expansión térmica similar y su constante dieléctrica moderada a los materiales de silicio (Si).
Tradicionalmente, los sorbetes de película gruesa están diseñados principalmente para sustratos de alúmina (Al2O3), pero la composición de estos sorbos es propensa a reacciones químicas cuando entran en contacto con sustratos de AlN, produciendo gases, lo que representa una seria amenaza para la estabilidad y el rendimiento de los circuitos de película gruesa. Además, dado que el coeficiente de expansión térmica del sustrato de AlN es menor que el del sustrato de Al2O3, la aplicación directa del proceso de lechada y sinterización adecuado para el sustrato de Al2O3 al sustrato de AlN conducirá al problema de desajuste de expansión térmica, lo que provocará afectar el funcionamiento del circuito. Por lo tanto, no es aconsejable copiar simplemente el sistema de materiales y el proceso de producción del sustrato de Al2O3 al sustrato de AlN. Este artículo describe en detalle el proceso de fabricación de la resistencia diseñada para sustrato de AlN, y estudia y analiza el desempeño de la resistencia.
medición del coeficiente de temperatura de resistencia
El coeficiente de temperatura de resistencia (TCR) representa el cambio relativo del valor de resistencia de CC de la resistencia a la temperatura de prueba con respecto al valor de resistencia de CC a la temperatura de referencia, es decir, el cambio relativo del valor de resistencia ΔTCR por cada 1 °C de temperatura. entre la temperatura de prueba y la temperatura de referencia:
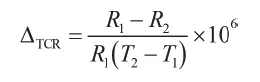
Donde: R1 es el valor de resistencia a la temperatura de referencia; R2 es el valor de resistencia a la temperatura de prueba. T1 es la temperatura de referencia; T2 es la temperatura de prueba.
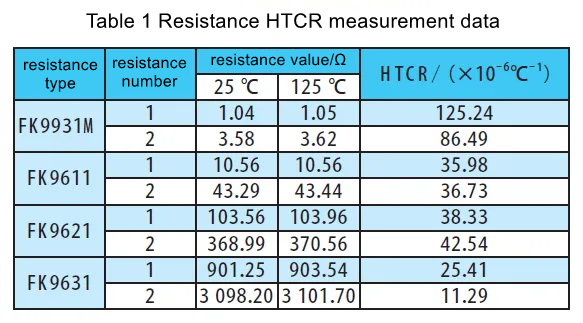
La resistencia de la película gruesa sobre el sustrato de AlN se midió mediante TCR. Los datos de la prueba del coeficiente de temperatura alta (HTCR) se muestran en la Tabla 1, y los datos de la prueba del coeficiente de temperatura baja (CTCR) se muestran en la Tabla 2. A partir de los datos de la prueba, se puede ver que el tamaño del diseño tiene un cierto efecto. sobre el coeficiente de temperatura de la resistencia. Todos los modelos de resistencia tienen un coeficiente de temperatura positivo en este sustrato de AlN, y el TCR de FK9931M es inferior a 150×10-6/â, y los modelos restantes son inferiores a 100×10-6/â.
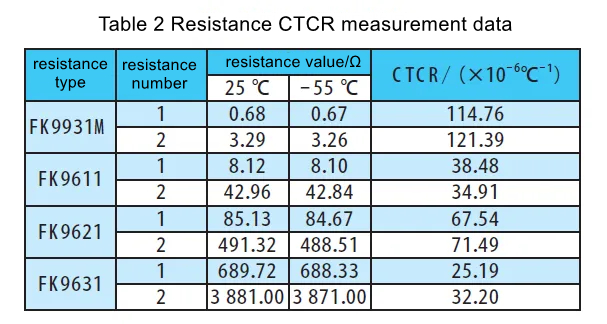
evaluación de estabilidad de resistencia
La resistencia puede considerarse como una estructura de red tridimensional compuesta de muchas cadenas conductoras. Cuando la capa de resistencia se somete a tensión, la cadena conductora más frágil se romperá o se alargará localmente, de modo que la capacidad conductora general se reducirá y el valor de resistencia aumentará. Por el contrario, cuando el coeficiente de expansión térmica de la capa de resistencia es obviamente menor que el del sustrato, la tensión dentro de la capa de resistencia es presión. Cuando la capa de resistencia se somete a presión, el contacto entre las partículas será más estrecho e incluso se agregará una nueva cadena conductora, lo que mejorará la capacidad conductora de toda la resistencia de película gruesa y el valor de resistencia se reducirá en la macro. nivel. Debido a que la resistencia de película gruesa está firmemente unida al sustrato y la liberación de tensión es lenta, el valor de la resistencia cambiará cuando la resistencia de película gruesa se almacene a una temperatura determinada. Cuanto mayor sea la diferencia entre el coeficiente de expansión térmica de la resistencia de la película gruesa y el sustrato, mayor será la tensión dentro de la resistencia de la película gruesa y mayor será la tasa de cambio de la resistencia de la película gruesa cuando se almacene a alta temperatura.
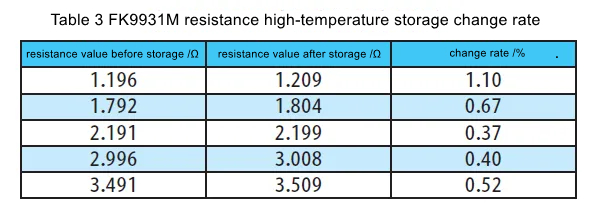
Según los diferentes tamaños de diseño, se imprimieron cuatro tipos de resistencias cuadradas en el sustrato de AlN y las resistencias se ajustaron mediante láser. Después del almacenamiento a temperatura de 150 ℃ y 1000 h, se comparó el cambio de los valores de resistencia antes y después del almacenamiento a temperatura. La resistencia de cada resistencia cuadrada mide el valor de resistencia de cinco resistencias. Como se puede ver en las Tablas 4 a 6, la tasa de cambio del valor de resistencia es inferior al 1,5% después de almacenarse a alta temperatura.

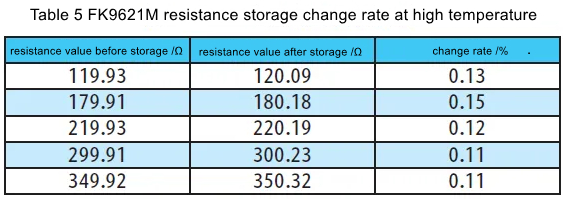
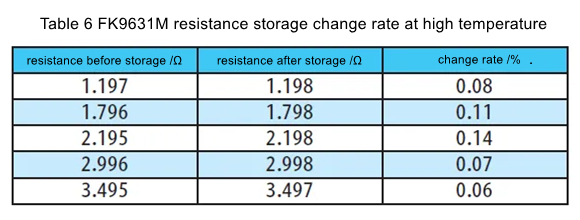
En resumen, con el rápido desarrollo de la tecnología de empaquetado de microelectrónica, la potencia y la integración de los componentes electrónicos han logrado un salto cualitativo, pero también han planteado desafíos sin precedentes para la eficiencia de disipación de calor de la placa de circuito. Los investigadores han respondido activamente a este desafío explorando y desarrollando una serie de materiales de sustrato cerámico con alta conductividad térmica, entre los cuales el nitruro de aluminio (AlN) destaca entre muchos materiales candidatos por su excelente adaptación a la expansión térmica y su constante dieléctrica moderada, y se ha convertido en el foco de la investigación actual.
En este artículo se analizan en profundidad las limitaciones de la tradicional suspensión de película gruesa en la aplicación de sustrato de AlN y se describe en detalle el proceso de fabricación de resistencia diseñado para las características del sustrato de AlN. Los resultados experimentales muestran que la resistencia de la película gruesa sobre el sustrato de AlN tiene un rendimiento estable, su coeficiente de temperatura está dentro del rango aceptable y la tasa de cambio de resistencia es muy pequeña después del almacenamiento a alta temperatura, lo que verifica la viabilidad y eficacia del proceso de producción. 53>
<54> <55>
<56>En el futuro, con más investigación y optimización del sustrato de AlN y su proceso de producción de soporte, tenemos razones para creer que el sustrato de AlN desempeñará un papel más importante en el embalaje de componentes electrónicos de alta densidad de potencia, y promover el desarrollo de la industria microelectrónica hacia un mayor rendimiento y una mayor integración.<57>