Con la continua evolución de la tecnología de embalaje de microelectrónica, la densidad de potencia de los componentes electrónicos ha aumentado significativamente, lo que ha resultado en un fuerte aumento en la generación de calor por unidad de volumen, lo que ha planteado estándares más estrictos para el rendimiento de la nueva generación de placas de circuito en términos de eficiencia de disipación de calor (conductividad térmica). En la actualidad, los investigadores están explorando y desarrollando activamente varios materiales de sustrato cerámico con alta conductividad térmica, incluidos nitruro de aluminio (AlN), carburo de silicio (SiC) y óxido de berilio (BeO). ). Sin embargo, los BEO tienen limitaciones ambientales debido a su potencial toxicidad; El SiC no se considera un material de sustrato ideal debido a su alta constante dieléctrica. Por el contrario, el AlN se ha convertido en una opción de alto perfil como material de sustrato debido a su coeficiente de expansión térmica similar al del silicio (Si) y sus propiedades constantes dieléctricas moderadas.
Tradicionalmente, las suspensiones de película gruesa se han desarrollado principalmente a base de sustratos de alúmina (Al2O3), pero los componentes de estas suspensión son propensos a reacciones químicas cuando entran en contacto con sustratos de AlN y producen gas, lo que representa una seria amenaza para la estabilidad y el rendimiento de las suspensiones gruesas. Circuitos cinematográficos. Además, debido a que el coeficiente de expansión térmica del sustrato de AlN es menor que el del sustrato de Al2O3, el uso directo del proceso de lechada y sinterización diseñado para Al2O3 en el sustrato de AlN conducirá a un desajuste de expansión térmica, lo que causará problemas. Por lo tanto, no es aconsejable simplemente trasplantar el sistema de materiales y el proceso de producción aplicable al sustrato de Al2O3 al sustrato de AlN. Este artículo se centra en el proceso de fabricación de resistencias sobre sustrato de AlN, analiza en profundidad el proceso de fabricación y evalúa y analiza el rendimiento de las resistencias en detalle.
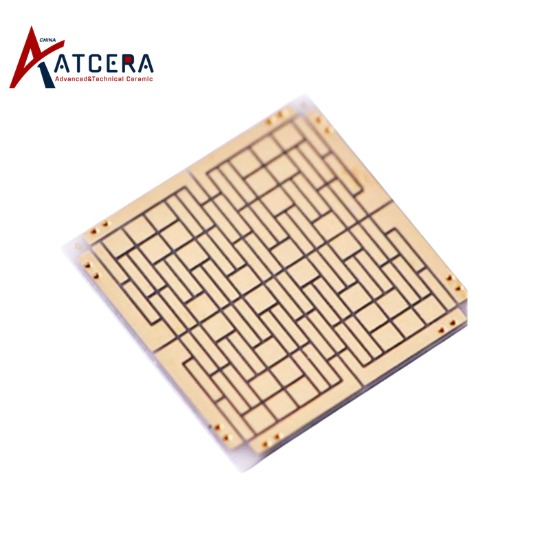
número de diseño de resistencia
Para determinar la relación entre el valor de resistencia del sustrato de AlN y el número de cuadrados de diseño, se diseñó la placa de prueba de resistencia (como se muestra en la Figura 4). La longitud de la resistencia varía de 500 a 2000 μm y el ancho de 500 a 2500 μm. Se imprimieron resistencias de cuatro tipos de resistencia cuadrada en el sustrato de AlN, la película se sinterizó a 850 ℃ y se midieron los valores de resistencia de las resistencias de diferentes tamaños de diseño.

Se mide el valor de resistencia de tres sustratos del mismo tamaño, se calcula el número cuadrado de diseño de la resistencia de tamaño, se promedia el valor de resistencia de las tres resistencias y se determina la relación entre el valor de resistencia y el número cuadrado de la Se forman cuatro tipos de resistencia cuadrada (como se muestra en la Figura 2).
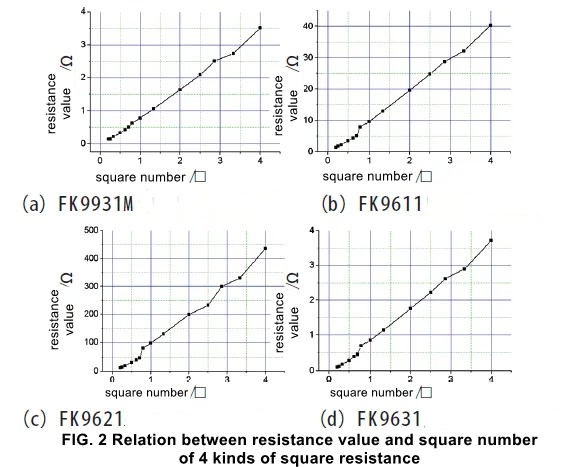
Cuando el valor inicial de la impresión de resistencia se diseña generalmente para que sea el 80% del valor nominal, es más propicio para mejorar el valor de ajuste y el rendimiento. Combinado con el diagrama de relación entre el valor de resistencia y el número cuadrado, se calcula la proporción de diseño de las cuatro resistencias cuadradas (ver Tabla 1).
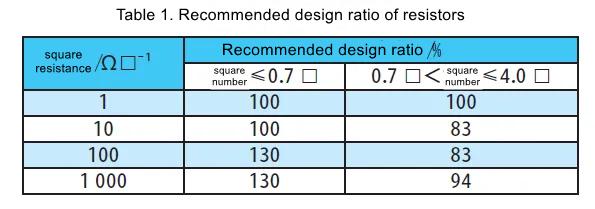
proceso de ajuste del valor de resistencia
En la producción real de resistencia de película gruesa, incluso si la composición de la lechada, el proceso de impresión, el espesor de la película, la cocción y la coincidencia de electrodos se controlan estrictamente, el error entre el valor de resistencia y el valor objetivo solo puede alcanzar ±20%. Para obtener el valor de resistencia con la precisión requerida basándose en la resistencia de película gruesa que se ha fabricado, el valor sólo se puede ajustar. En términos de mejorar la precisión del valor de rendimiento y resistencia, el ajuste del valor es una tecnología esencial e importante.
Los parámetros del proceso de ajuste de resistencia en el sustrato AlN son los siguientes: corriente 14,5 A, frecuencia Q 2500 Hz, distancia del punto láser 150. Según el análisis de la forma de las marcas de corte después del ajuste, el ancho de las marcas de corte de resistencia de los cuatro Los tipos de resistencia cuadrada son superiores a 30 μm y no hay resistencia ni restos de sustrato en las marcas de corte, lo que cumple con los requisitos pertinentes de los documentos de inspección.
En resumen, con el rápido desarrollo de la tecnología de empaquetado de microelectrónica, los requisitos para la eficiencia de disipación de calor de la placa del circuito están aumentando, lo que promueve la investigación y el desarrollo de materiales de sustrato cerámico de alta conductividad térmica. Entre ellos, el nitruro de aluminio (AlN) se destaca entre muchos materiales candidatos debido a su superior expansión térmica y sus características constantes dieléctricas moderadas, y se ha convertido en una opción popular para una nueva generación de materiales de placas de circuito. Sin embargo, la singularidad del sustrato de AlN también requiere que hagamos los ajustes y optimizaciones correspondientes en la selección de la suspensión de película gruesa y el proceso de producción para evitar los problemas causados por el mismo sistema de material y proceso que el sustrato de Al2O3.
En este artículo se estudia en profundidad la tecnología de fabricación de resistencia en sustrato de AlN mediante el diseño de la placa de prueba de resistencia, la medición y el análisis de la relación entre la resistencia y el número cuadrado y la exploración de la tecnología de ajuste de resistencia. Los resultados muestran que se puede obtener resistencia con rendimiento estable y alta precisión sobre sustrato de AlN diseñando la relación de tamaño de la resistencia de manera razonable y controlando los parámetros del proceso con precisión. Los resultados de esta investigación no solo brindan soporte técnico para la aplicación del sustrato AlN en el campo del empaque de microelectrónica, sino que también brindan una solución efectiva para el problema de disipación de calor de los componentes electrónicos de alta densidad de potencia en el futuro. Con el progreso continuo de la tecnología, la mejora del sustrato de AlN y su proceso de producción de soporte inyectarán nueva vitalidad al desarrollo sostenible de la industria microelectrónica.