En comparación con otras membranas cerámicas de óxido (alúmina, óxido de titanio, circonio, etc.), el tubo de membrana de carburo de silicio tiene mayor hidrofilicidad, permeabilidad, resistencia a la contaminación y estabilidad química. La temperatura de sinterización de la membrana cerámica SIC está estrechamente relacionada con la tecnología de sinterización, y la tecnología de sinterización común incluye tecnología de recristalización, tecnología de conversión de precursores cerámicos y tecnología de sinterización por reacción in situ.
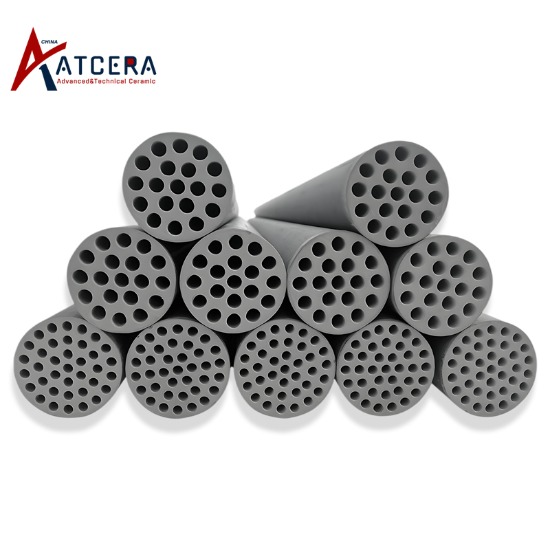
Tecnología de sinterización por recristalización
La tecnología de sinterización por recristalización se refiere a la realización de la reunión de partículas de SIC de acuerdo con el mecanismo de migración de la fase gaseosa de evaporación-condensación bajo sinterización a alta temperatura. Este proceso no implica demasiada reacción química, el tamaño de los poros se ve muy afectado por el tamaño del polvo de la materia prima, la estructura de poros de la membrana de carburo de silicio obtenida es uniforme y el factor de zigzag es bajo. Dado que el carburo de silicio tiene buena estabilidad a alta temperatura, alta presión y un amplio rango de pH, generalmente se utilizan aditivos de sinterización y distribución bipico del polvo de carburo de silicio para reducir la temperatura de sinterización durante la recristalización. El tubo de membrana de carburo de silicio preparado mediante tecnología de sinterización por recristalización tiene una alta estabilidad química, pero su temperatura de sinterización es alta (> 1800 ℃), el consumo de energía es grande, se requiere protección de atmósfera inerte durante el proceso de sinterización y el equipo es extremadamente estricto. Además, para eliminar el posible carbón residual en el poro, una vez completada la sinterización, la oxidación de la superficie debe realizarse en una atmósfera de aire por debajo de 800 °C, lo que complica el proceso de preparación.
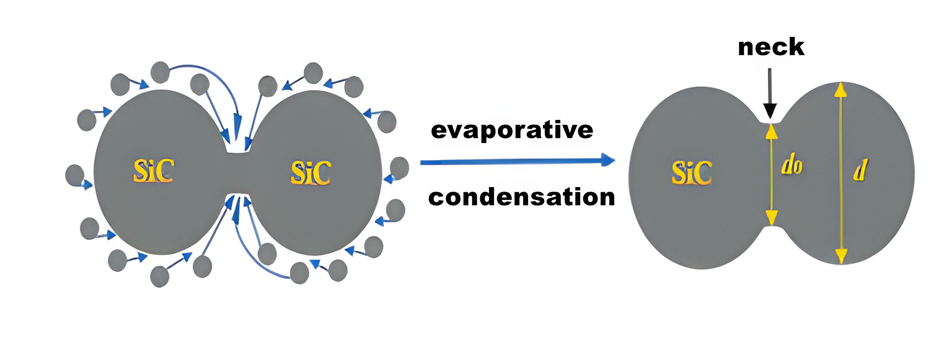
Diagrama de recristalización de alta temperatura de SiC
Tecnología de conversión de precursores cerámicos
La tecnología de conversión de precursores cerámicos se refiere al craqueo de polímeros orgánicos que contienen silicio (como resina de silicona, policarbosilano, etc.) en una atmósfera inerte y un cierto rango de temperatura (1100-1600 ℃) para formar una fase de unión entre agregados de carburo de silicio. , para preparar CA y una cierta resistencia mecánica de la membrana cerámica de carburo de silicio. La tecnología de conversión de precursores cerámicos tiene bajos requisitos de temperatura de sinterización, lo que favorece la reducción del consumo de energía. Sin embargo, su materia prima es un alto contenido de polímeros y el proceso de sinterización requiere una atmósfera anaeróbica, lo que tiene las desventajas de un alto costo y un proceso complejo, que no favorece la producción industrial. Para seguir desarrollando y optimizando el potencial de aplicación de la tecnología de conversión de precursores cerámicos para la producción de membranas, es necesario centrarse en la reducción de costos y la regulación de la microestructura (tamaño de poro, porosidad y espesor de la membrana).
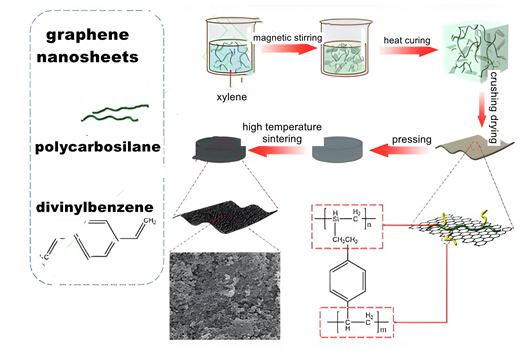
Preparación de membrana cerámica de carburo de silicio mediante tecnología de conversión de precursores cerámicos.
Tecnología de sinterización por reacción in situ
La tecnología de sinterización por reacción in situ se refiere a la adición de aditivos de sinterización a las partículas agregadas de carburo de silicio bajo una atmósfera de aire, de modo que sea mucho más baja que la temperatura de sinterización de la membrana cerámica de carburo de silicio en fase pura (1350-1550 ℃) para generar óxido de silicio. y luego la reacción in situ con el agente de sinterización para formar una conexión de cuello. Los aditivos de sinterización habituales son principalmente óxidos metálicos, como alúmina, óxido de itrio y circonio. En el proceso de reacción, la mullita, la cordierita y otros óxidos multicomponentes se convierten en la fase de unión de la conexión del cuello entre las partículas. La adición de estos aditivos de sinterización favorece el cambio del límite de grano y la energía superficial del agregado SIC, acelerando así la tasa de difusión de masa en el proceso de sinterización y reduciendo el costo de sinterización. La tecnología de sinterización reactiva in situ puede reducir eficazmente la temperatura de sinterización del SIC, pero aún es necesario reducir el proceso de preparación de la membrana.
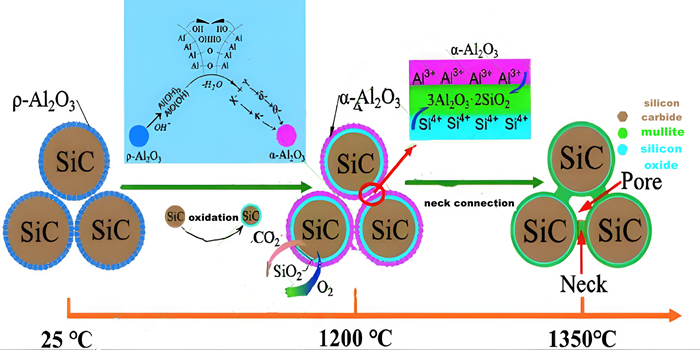
Diagrama esquemático del proceso de sinterización de cerámicas porosas de carburo de silicio unidas con mullita preparadas mediante la técnica de sinterización reactiva in situ
Para mejorar aún más el potencial de aplicación industrial del tubo de membrana de carburo de silicio, se puede considerar desde el punto de vista de la reducción de costos y la mejora del rendimiento. Por ejemplo, para reducir el coste, se pueden buscar precursores de polímeros de bajo coste para preparar membranas de carburo de silicio de separación de gases con tamaño de poro pequeño; También puede optimizar la combinación de aditivos de sinterización, reducir la temperatura de sinterización y ampliar aún más el rango de aplicación de la tecnología de co-sinterización.
Con la preocupación mundial por la protección del medio ambiente, la demanda de tecnología de filtración y separación de alto rendimiento se ha vuelto cada vez más urgente, lo que brinda valiosas oportunidades para el desarrollo y la aplicación de tubos de membrana de carburo de silicio. En el futuro, todavía se necesitan muchos recursos para resolver los problemas de la tecnología de producción y preparación de membranas cerámicas inmaduras, de modo que la tecnología de separación de membranas cerámicas de carburo de silicio pueda tener aplicaciones más prácticas.