En la industria electrónica actual que cambia rápidamente, los materiales de sustrato cerámico son una base clave para soportar dispositivos electrónicos de alto rendimiento, su rendimiento y características afectan directamente el rendimiento general y la confiabilidad de los productos electrónicos. Desde las primeras cerámicas de alúmina hasta las posteriores nitruro de aluminio, nitruro de silicio y otros materiales nuevos, el desarrollo de materiales de sustrato cerámico ha sido testigo del progreso y la innovación continuos de la ciencia y la tecnología. Este artículo lo llevará a explorar las ventajas únicas y las perspectivas de aplicación de estos materiales de sustrato cerámico, especialmente cómo las cerámicas de nitruro de aluminio y nitruro de silicio se destacan en la solución de disipación de calor de dispositivos de alta potencia y entornos de disipación de calor de alta intensidad con su excelente rendimiento. Y convertirse en un material importante e indispensable en la industria electrónica moderna.
Sustrato de alúmina, como pionero del sustrato cerámico, ha sido desarrollado con éxito por Siemens en Alemania desde 1929 y entró en producción industrial en 1933, con su bajo precio, excelente estabilidad, buen aislamiento y propiedades mecánicas, ha ocupado durante mucho tiempo una posición dominante en una amplia gama de aplicaciones. Sin embargo, su conductividad térmica relativamente baja y su coeficiente de expansión térmica que no coinciden con el Si limitan su desarrollo posterior en productos electrónicos de alta potencia, y se utiliza principalmente en el campo del empaquetado de circuitos de bajo voltaje y baja integración.
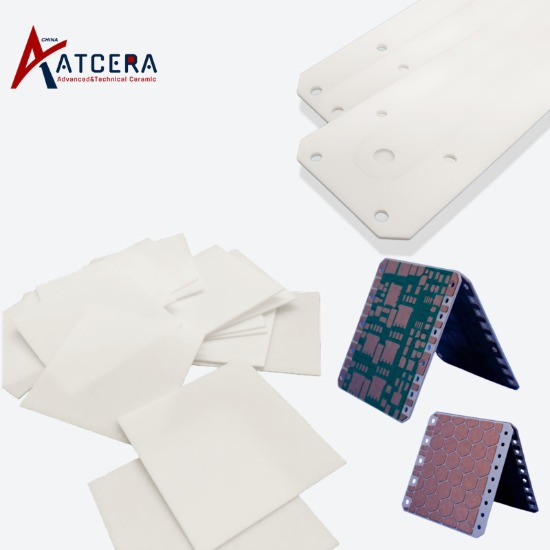
Posteriormente, aunque los sustratos de BeO destacaban por su alta conductividad térmica, el problema de la toxicidad se convirtió en un obstáculo insuperable, que no sólo fue prohibido en Japón, sino también severamente restringido en Europa, dificultando en gran medida su amplia aplicación. .
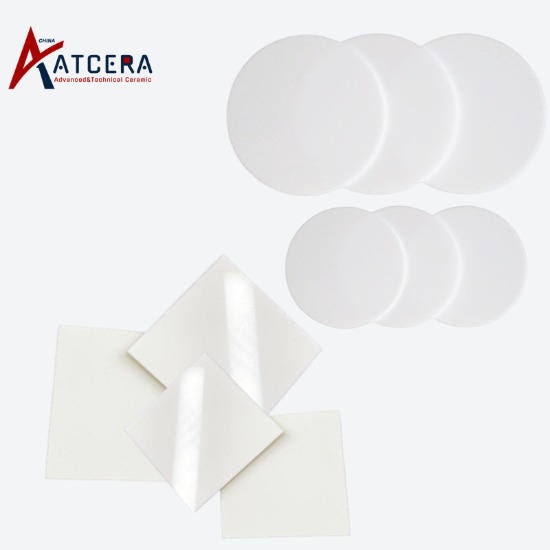
Por el contrario, aunque el monocristal de SiC tiene una sorprendente conductividad térmica, la conductividad térmica de las cerámicas policristalinas de SiC disminuye significativamente debido a la diferencia en la orientación del grano, sumado a un pobre rendimiento de aislamiento y una alta pérdida dieléctrica, lo que hace que la investigación avance en el campo de Los materiales de la placa de circuito son lentos.
En este contexto, las cerámicas de nitruro de aluminio y nitruro de silicio están emergiendo gradualmente con sus ventajas de rendimiento únicas. Sustrato de nitruro de aluminio con su excelente alta conductividad térmica (valor teórico de hasta 320 W/(m·K), la conductividad térmica del producto comercial también está entre 180 W/(m·K) ~ 260 W/(m·K) ) se ha convertido en un material clave para resolver el problema de disipación de calor de los dispositivos de alta potencia y, desde la década de 1980, bajo la promoción de los países desarrollados, especialmente Japón, se ha convertido rápidamente en una nueva generación de materiales de embalaje cerámicos avanzados. Su alta resistencia mecánica y estabilidad química garantizan un funcionamiento estable en entornos hostiles.
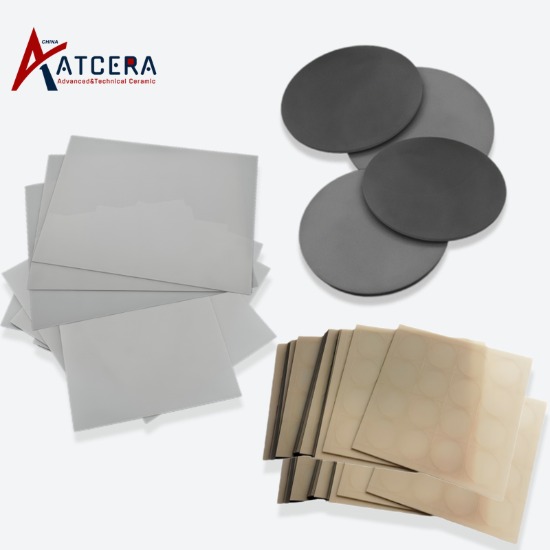
Sustratos de nitruro de silicio, después de experimentar la etapa inicial de conductividad térmica subestimada, a través de la investigación científica y la optimización de procesos, su conductividad térmica ha mejorado significativamente, superando los 177 W/ (m·K), manteniendo un coeficiente de expansión térmica muy bajo (3,2 × 10 − 6/â), convirtiéndose en uno de los materiales de sustrato cerámico más excelentes con un rendimiento integral. Su excelente resistencia a la flexión y al desgaste muestran una extraordinaria competitividad en entornos de disipación de calor de alta intensidad.
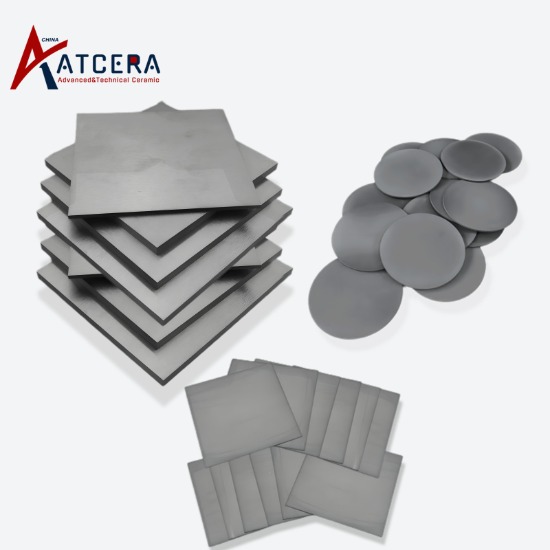
En resumen, las cerámicas de nitruro de aluminio son la mejor opción para la disipación de calor de dispositivos de alta potencia debido a su alta conductividad térmica y coeficiente de expansión térmica que coinciden con los materiales semiconductores. Las cerámicas de nitruro de silicio, con sus amplias ventajas de rendimiento, lideran el camino en entornos térmicos exigentes. Juntos, los dos llevan a los materiales de sustrato cerámico a un mayor rendimiento y una gama más amplia de aplicaciones.