La soldadura fuerte es el proceso más importante en el proceso del sustrato de nitruro de silicio AMB, y la preparación del metal de aporte para soldadura fuerte activa y la soldadura fuerte con metal activo son los puntos clave y difíciles en la actualidad.
Ti, Zr, Hf, V, Nb, etc. son elementos metálicos activos comunes que pueden infiltrarse en sustratos de nitruro de silicio superficies y se utilizan ampliamente para el sellado activo entre cerámica y metales. Entre ellos, la aleación Ag-Cu-Ti con Ti como elemento activo es el metal de aportación activo más estudiado y más utilizado. Puede humedecer la mayoría de las superficies cerámicas a una temperatura de 800 ~ 950 ℃, y el cabezal de soldadura tiene alta resistencia y rendimiento estable, de modo que se puede realizar mejor el sellado entre cerámica y metales, cerámica y cerámica.
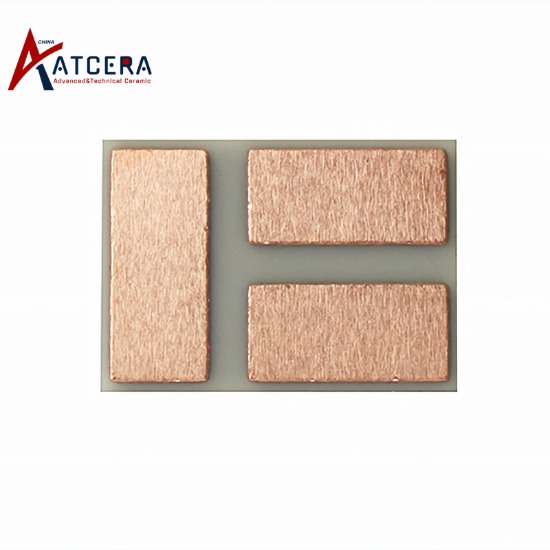
El uso de metal de aportación activo Ag-Cu-Ti incluye las siguientes cuatro formas, que varían según la forma del elemento Ti y la combinación de metal de aportación:
a. Pasta previamente recubierta de polvo de Ti (o TiH, polvo) y luego agregue soldadura preformada (generalmente soldadura de aleación Ag72Cu28);
b. Se deposita una capa de película de Ti sobre la superficie cerámica con PVD (deposición física de vapor) o CVD (deposición química de vapor) por adelantado, y luego se agrega metal de aportación Ag-Cu.
c. Utilice soldadura Ag-Cu-Ti;
d. Utilice pasta de soldadura Ag-Cu-Ti.
Cuando se utiliza metal de aportación activo de plata, cobre y titanio para preparar el sustrato de nitruro de silicio AMB, las principales causas de los huecos interfaciales son las siguientes:
1. Calidad de la superficie de las materias primas: los rayones, picaduras, oxidación, contaminación orgánica en la superficie de la cerámica y el cobre libre de oxígeno antes de la soldadura tendrán un impacto negativo en la humectación y dispersión de la soldadura, lo que generará un riesgo potencial de huecos en la interfaz soldada. .
2. Calidad de impresión de soldadura: en el proceso de impresión de pasta de soldadura de área grande, es fácil tener el problema de fugas de pasta de soldadura e impresión desigual, y una vez que la soldadura se derrite, conducirá directamente a la formación de agujeros.
3. Desactivación de elementos activos: el elemento activo Ti en la soldadura en pasta AgCuTi es muy sensible al oxígeno y, a menudo, se requiere que el grado de vacío sea mejor que 10-3 Pa en el proceso de soldadura fuerte a alta temperatura. Si el grado de vacío no puede cumplir con los requisitos de soldadura, el Ti se oxida y desactiva, y la soldadura no puede mojar la superficie cerámica, lo que provocará una gran área de soldadura, fugas de soldadura y otros fenómenos.
4. Gas volátil en pasta de soldadura: en el proceso de soldadura fuerte, el gas volatilizado en la pasta de soldadura será envuelto por el fundente para formar burbujas; además, la reacción de los ácidos orgánicos y los óxidos metálicos en el fundente también producirá burbujas. A medida que la reacción de las burbujas aumenta gradualmente, las burbujas descargadas dejarán poros densos en la superficie de la pasta de soldadura, y las burbujas no descargadas también permanecerán en la interfaz de soldadura fuerte con el proceso de fusión y solidificación de la soldadura. Formando un vacío.
5. Parámetros del proceso de soldadura fuerte: el metal de aportación de soldadura fuerte activo Ag-Cu-Ti suele estar por encima de 800 ℃ para humedecer la superficie de Si3N4, si la temperatura de soldadura fuerte es demasiado baja o el tiempo de retención es demasiado corto, la reacción entre el Ti y la superficie cerámica no es suficiente, lo que provoca que el metal de aportación de soldadura fuerte no pueda mojar completamente la superficie cerámica.
En resumen, la soldadura fuerte es crucial para los sustratos de nitruro de silicio AMB, con la aleación Ag-Cu-Ti como principal metal de relleno activo debido a su capacidad para humedecer cerámicas a 800 ~ 950 °C y formar uniones fuertes. Sin embargo, los huecos interfaciales son un problema importante causado por factores como la calidad de la materia prima, la impresión de la soldadura, la desactivación del elemento activo, los gases volátiles y los parámetros de soldadura inadecuados. Para lograr uniones de alta calidad, es esencial abordar estos desafíos mediante una preparación refinada, técnicas mejoradas, condiciones optimizadas y un control de procesos mejorado.